Set to revolutionise the industry!
The Taiwan-based company is known for more than 100 different models that include basic models such as single jersey, rib, interlock, fleece and terry as well as sophisticated models such as single knit jacquard, double knit jacquard, rib-mesh transferred jacquard, fishnet jacquard, float plaiting (weave knit) jacquard, etc. Established in 1977, Pailung has been a name to reckon with globally in the knitting industry. The company’s Chairman James Wang can be credited with much of its success over the last five decades since he took over from his father in the 1980s. High Productive Single Jersey Machine
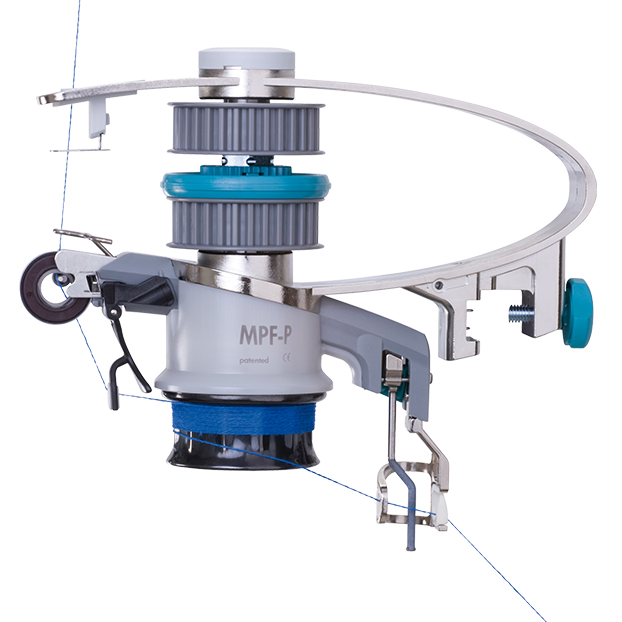
In an exclusive interaction, Mr. James Wang, who joined the business in 1985, recollected how knitting was hardly an option for companies globally in the 1980s.
“Today, however, knitting as a manufacturing process has come a long way thanks to all the innovation and research and development by knitting machinery manufacturers worldwide to make this a compelling option for textile manufacturing. Pailung has definitely been pioneer in this effort with more than 525 patents to its credit.”
Pailung initially had its manufacturing facility in Taipei city and later on moved to Ruifang district in 1997. Now, the company is all set to launch its latest technology at ITMA Milan 2023.
Some of the key milestones in this eventful journey of the company include:
Highlighting some of the defining moments for the company in the last five decades, Wang said: “We are known for our wide range of products. Pailung has developed more than 100 different models that include basic models such as single jersey, rib, interlock, fleece and terry as well as sophisticated models such as single knit jacquard, double knit jacquard, rib-mesh transferred jacquard, fishnet jacquard, float plaiting (weave knit) jacquard, etc.”
“The second key success factor is sales and service channels worldwide. We have sales and service channels including overseas branches, subsidiaries and agents in more than 40 countries. These sales and service channels not only provide sales activity but also technical backup service,” he added.
Customers are rest assured that when they buy a machine from Pailung they will definitely get technical support while the machine is running. The third key successful factor is consistent investment in research and development and open innovation lab (OIL). OIL has accumulated more than 4,500 fabrics’ DNA and continues to develop 200 state-of-the-art fabrics yearly. This is to provide customers with:
Pailung is located in Taipei city and has on board 243 skilled employees. Its machines are available in around 72 countries through over 40 branches and agents and the company has a capacity of producing 150 machines per month on an average. Also, in 2009, Pailung Machinery Mill Co. Ltd. acquired the historic Vanguard Supreme Machinery Company, thus forming Vanguard Pailung. With offices located in Mexico, Honduras, Colombia and Brazil, it has established the largest presence of its kind for any machine manufacturer in the western hemisphere. Vanguard Pailung’s headquarters are in Monroe with 80 employees on board.
Sharing details about the products and solutions offered by Pailung for the global market, James Wang stated, “We are aiming for energy-saving and carbon-reducing products and we do believe our customers are also following it. Through persistent research and development, Pailung’s fabric technology is continuously reiterated and improved upon, moving the textile industry forward at a sustainable rate. Pailung’s OIL specialty is our unique relationship with the machine. Open access to the machine makes it possible to experiment in ways few others can.” Answering a question on the key global markets, Wang said, “With our reach we sell in about 40-50 countries per year of which the top markets are India, Turkey, Bangladesh, Pakistan, Vietnam, Indonesia, China, Thailand, Honduras and Egypt.”
Pailung has always been known for its focus on innovation. Elaborating on the same, James Wang said, “As a knitting machinery innovator and fabric innovation leader, we are tuned into the needs of the knitting market. Here are some examples of how we have cooperated with the brand and fabric manufacturers to provide the right kind of solutions. Pailung’s Open Innovation Lab produces an innovative new textile solution for yoga apparel use. The solution, which involved creating a new fabric technology, altered the original yarn structure in a way that both blocked light and transparency while retaining fabric flexibility and sheer. This new fabric technology has since been adopted by one of the world’s leading yoga apparel brands.”
Some of the company’s leading products include:
StayFleece™: Fleece has always been popular for its comfort and warmth and unfortunately has always shrunk after a wash. One of the solutions presented by Open Innovation Lab was to integrate polyester yarns into a fleece fabric technology which would virtually eliminate shrinkage. However, for the retailer, visible polyester yarns presented a brand quality issue. Pailung solved this problem by developing a machine that could not only integrate polyester yarns but hide them as well, giving the finished fabric technology a higher quality appearance and feel.
WeevKnit™: This was an experiment to discover a fabric technology as strong as a weave but as comfortable as a knit. WeevKnit knitting machines and fabric technologies help designers, brands and manufacturers explore a whole new world of possibilities.
StyleSpacer™: By working with Pailung’s machine development team and Open Innovation Lab, a new way to integrate jacquard design techniques into a spacer fabric technology was developed, not only changing the way designers could think about bra design, but also providing a lower cost alternative to previously existing technology.
MultiFleece™: This is the company’s most innovative fleece fabric technology. With double-sided design capabilities, you can create jacquard patterns on both sides of the fleece, allowing you to explore a new range of opportunities.
SwissFleece™: SwissFleece gives you design on one side with soft brushed fleece on the other. SwissFleece is the perfect solution for designers and brands looking to cut the cost and time associated with fleece applications.
ShupperKnit™: Every sneaker brand in the world is racing towards developing knitted uppers using flat knitting machines. While these machines are able to produce countless shoe upper designs and patterns, production efficiency is disappointingly low — each machine is able to produce only 20-30 pairs of shoe uppers per day, and this only make sense for producing high-end sneakers. After a leading sneaker brand and its manufacturer approached Pailung for help to speed up their production process, the company worked with them to build a small circular knitting machine from the ShupperKnit series — accelerating production three-fold. This solution increased productivity and introduced a new line of mid-range sneakers, enabling them to offer a range of sneakers and gain market share.
Visitors to Pailung’s booth at ITMA 2023 can look forward to its newest technology. Pailung’s fabric technology is continuously reiterated and improved upon, moving the textile industry forward at a sustainable rate.
In June 2023, Pailung will exhibit the newest technology AlterKnit™ at ITMA in Milan, alongside the portfolio of advanced, circular knitting machines with high speed which can increase the capacity and aid in the development of new fabric technologies such as three layers of high-pile fabric without bonded gel, higher density and also two colours on both sides and system innovations, including the MES and fabric defect detection systems. Also, Pailung will be organising in-house seminars to highlight the latest knitting technology in Hall 2, Booth C 101.
Pailung has always been at the forefront when it comes to Industry 4.0 with its automation and digitisation initiatives. Spelling out its key initiatives on this front, James Wang said: “After Pailung launched the Industry 4.0 solution (POMS + MES) for circular knitting firm, this has won the trust and adoption of customers. The company constantly listens to customers’ voices, responds to their professional feedback and suggestions, updates the entire solution and is closer to customers’ needs.”
“These updates are not only for modification of the POMS, i.e., the factory management system but also for a deeper integration between MES machines and systems”, he said.
“For example, the customer hopes that the system can count how many kilograms of fabric the machine has knitted rather than how many revolutions the machine has run because fabric orders are calculated by kilogram. In addition to calculating the weight of grey fabric, the MES machine can also calculate the weight ratio of all yarns contained in the current fabric, including spandex. This is very important for knitting mills focusing on yarn consumption and fabric quality management,” he added.
“In response to demand, we have modified the machine so that it has the function of calculating grey fabric weight and can transmit it to the POMS for production reports. However, Pailung does not stop at meeting customers’ needs.”
“For example, in the stage of fabric development or mass production, it can calculate the yarn consumption ratio after the machine is automatically adjusted or manually adjusted to ensure that the grey fabric quality of each MES knitting machine is consistent and meets the order requirements. While we respond to customer needs, Pailung also consistently introduces new technologies into MES machines, such as programmable continuously variable transmission (CVT) take-up system. The traditional take-up system uses gear transmission or a variable resistance knob to realise roller speed change. However, gear transmission can only be manually shifted when the machine stops”, Wang said.
“The operator needs to repeatedly start and stop the machine to find the right gear combination. Although the variable resistance knob can adjust the roller speed while the machine is running, it cannot accurately reproduce the same roller speed on each machine because it is an analog control, not a digital control. Pailung CVT take-up system uses a digital control method. The operator can change the roller speed by simply entering a number and get the same speed even on different machines. It can provide more subtle speed changes, and can set different winding speeds during the completion of a roll of fabric, which is more suitable for winding fabrics that are sensitive to tension like four-way stretch fabric,” Wang further said.
“The above is part of the results of intense research and development in the Industry 4.0 project in the past four years. In addition, Industry 5.0 and innovative fabrics also have related achievements. For example, the fabric defect detection technology is related to Industry 5.0. Pailung’s solution has high-speed identification. The entry-level version supports SF 900 for three-end fleece detection, low energy consumption (36 W power consumption) and the minimum number of cameras for easy maintenance (one camera for single jersey), etc. Pailung will deliver circular knitting machines with eyes to help customers check the quality of fabrics at the first time, 24 hours a day,” he added.
Continuing further on the topic, Wang remarked: “Pailung not only thinks about topics such as Industry 5.0, automation and digitalisation but also thinks about the related technologies of these topics and how to apply them to products so that customers can achieve success in profitability and sustainability. Although the energy and water resources used in the knitting are the least in the garment industry, Pailung still contributes to sustainability.”
“For this reason, Pailung has developed the K Plus HS series to provide a higher ratio of kilogram fabric per kWh. For example, under the same cylinder size, gauge, voltage, yarn type and stitch length for single jersey fabric and at the same kWh, the K Plus HS series SF 1350 has 40% more productivity than the previous generation SF 960. And at this high speed, the fabric defect detection system can continuously detect the quality of the fabric to avoid the waste of yarn caused by defects”, he added.
The company’s products and solutions have been contributing immensely to sustainable manufacturing too. “Improving the energy efficiency of knitting machinery is only part of sustainable manufacturing. It is another philosophy to reduce air-conditioning energy consumption by improving fabric performance. Pailung launched three kinds of faux fur fabric series knitting machines in order to improve the thermal performance of various forms of faux fur fabrics, and at the same time reduce the energy consumption of fabric processing by removing the laminating and pile trimming processes through innovative weaving methods,” James Wang explained.
“The third philosophy is to reduce the possible pollution of water and fish food chains caused due to damaged glue particles of fabric screen printing. Pailung’s latest KSAKCJB3-W | KDAKCJB, single | double jersey jacquard series adopts the latest AlterKnit technology to provide new choices of colour jacquard, especially KDAKCJB, which provides extremely lightweight double jersey with up to four-colour jacquard. The production capacity is also twice as much as that of the traditional four-colour computerised jacquard. The AlterKnit fabric has good colour fastness and no printing glue degradation problem,” he elaborated.
“The last philosophy is to improve factory management, reduce the energy and yarn consumed in trial production, and give uniformity to the weaving quality of different machines of the same specification. The Pailung POMS + MES system digitises the machine adjustment method of weaving fabric and adjusts the trial production of knitting machines. POMS can also be used to deploy fabric loop length, cam box height, fabric take-up speed, etc. for a large number of knitting machines of the same specification at the same time, thus reducing human adjustment errors,” he said.
Coming out of the pandemic and under the impact of the war, James Wang feels that business at Pailung is a little bit slow as compared to last year.
“We expect it to pick up after the second season,” he said. Yet, despite the challenges, the company has always been ahead of the curve. “We provide better service and new innovations compared with our competitors. The Open Innovation Lab will make the new sample of more than 200 designs yearly. And from research and development, they will make new innovations with new patents every year. Not only will our customers find new things emerging from our company, brand buyers will also benefit from the products and solutions we will continue to offer,” he said.
The company is marching towards celebrating 50 glorious years in the business. So, what is the future vision that James Wang has set for Pailung? Replying to this question, he said, “The top three points for Pailung are making a difference, helping high-speed production and digital transformation. As regards differentiation, we always keep eye on the market and quickly tap into our innovation base to create new products and solutions. Take, for example, our latest innovation AlterKnit which is a total solution to manage sustainability from the yarn to the final product. AlterKnit improves knitting efficiency by reducing scrap fabric that would be wasted. When applying designs to fabric, AlterKnit requires fewer steps to create a finished fabric. This reduces the labour involved as well as overall costs and energy use,” he observed.
“Secondly, the speed of manufacturing can increase the final capacity with less energy use. The high speed reduces machine parts’ energy consumption for different fabrics. For instance, the single knit machine SF 1350 and double knit SF 1200 for plain single jersey and lycra as well as SP 900 for fleece and terry SP 900,” Wang elaborated.
“Finally, the focus is also on attaining greater accuracy and efficiency in quality control. For digital transformation we aim for stable quality and reduction in errors during the knitting process. Take the mailing system, for example, The Pailung Online Management System (POMS) allows the technician to control multiple knitting machines from a single computer. All workflows from production to order scheduling and machine monitoring can be performed remotely using this central system,” Wang shared.

Circular Knitting Machine Design “All knitting details for the fabric that are saved in the KFMS along with their corresponding parameters can be accessed through the POMS. From there the technician can select a fabric, schedule production and monitor each knitting machine’s progress — all via the dashboard on their computer. Also combining our latest innovation FDD (fabric defect detection system), knitting machines can be shut down immediately whenever a fabric defect is detected. This minimises the amount of defective fabric that goes to waste, reducing the manufacturer’s losses and the environmental impact of textile manufacturing. We can make the error come down to ±0.5 or even lesser,” Wang added. “Pailung is not only a knitting machine producer but also a fabric developer, dedicated to helping brands, designers and manufacturers develop innovative fabric technologies that boldly transform results,” he concluded.